Eー23.対策を強化すること
- Yアカデミー
- 7月1日
- 読了時間: 6分
更新日:7月2日

『対策の強化』について解説します
事故・トラブルを防ぐことができない、あるいは効果が低い対策を一生懸命実施しても、それは自己満足でしかありません。まずは原因を追究し、その原因が潰せる対策を講じることによって初めて効果を発揮します。原因の追究に関しては別の記事で「WHYツリーを活用することにより真因に辿り着くことができること」は解説していますので、ここでは原因が潰せる対策、つまり対策の強化をどのような視点で考えればよいかについて解説します。
1.対策を強化するうえでの視点
1.3つの視点で対策を検討する
対策は「無くすこと」「機械で対応すること」「人で対応すること」の3つの視点から検討していきます。
まずは、この3つの視点をベースに、”できる” ”できない”を問わず、防止対策として考えられるものを考えられるだけ考えていきます。
このとき、一人で考えると、パターン化した思考が新たな良案を見落としてしまう可能性があるため、ブレインストーミングを活用して、できるだけ多くのアイデアを集めます。
【注意事項】
食品安全上、異物混入は極めて重要なリスクに位置づけられます。
従って、”金属異物”の混入を防ごうと思えば、まずは『金属片が発生するものは使わない(=無くす)』が大前提になります。
しかしながら製造工程においては数多くの金属が使用されていますので、全く使わないわけにはいきません。
従って、金属片が発生したとしても『金属検出機で検知させる(=機械で対応)』ことで対応します。
しかしながら、金属検出機には検出感度がありますので、必ずしもすべての金属を検出させることは不可能です。
従って、工程で金属片を発生させないことが重要になり、そのためには製造機械の取り扱いに注意する必要がありますので、『管理運営ルールを策定し、教育をすることで金属片を出さないようにする(=人で対応)』ことも重要になります。
このように対策は3つの視点で検討していくと効果が高まります。

2.対策を4Mの視点で展開する
上記”3つの視点”を工場のMECEである4M、「ヒト」「原材料」「機械設備」「方法」で整理していきます(縦軸に4M、横軸に3つの視点を記入した表を作成するとわかりやすくなります)。
別の記事で工場のMECEは4Mであると解説しました。
従って、事故・トラブルの真因は、このいずれかにあると考えられますので、対策も4Mを基準に検討し、組み合わせていくことでリスクを減らすことが可能になります。
【注意事項】
事故・トラブルは、定常状態よりも非定常状態で発生します。
従って、縦軸に4M、横軸に3つの視点を記入した表を作成する際は、”定常” ”非定常”の項目を設けることをお薦めします。
また所謂「はじめて」「ひさしぶり」「へんこう」の3H作業時に事故やトラブルが発生しやすい傾向にありますので、”非定常”の項目としては、「3Hの有無」も忘れないよう、但し書きしておくとよいです。
ここでは対策の強化策として解説していますが、原因を追究する際もこの表を活用し、調べることにより感度が高まります。
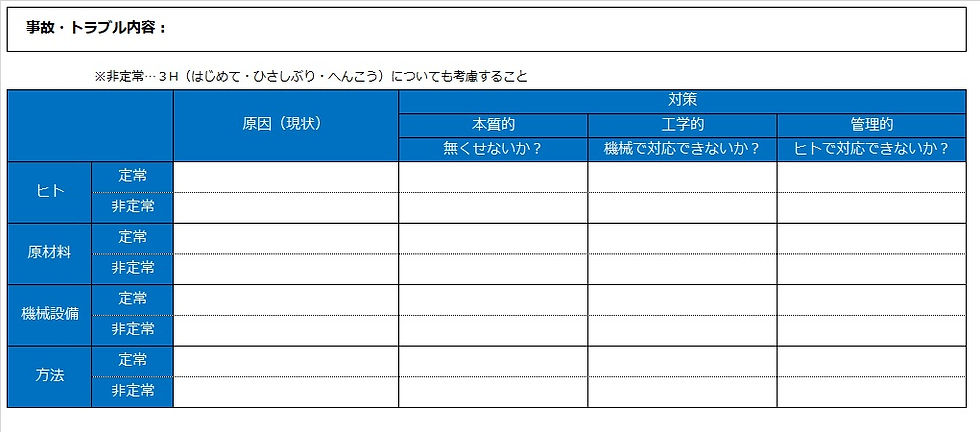
なお、まずは”考えられ得るだけ、多くの対策を考える”と記載しましたが、当然ながらすべての対策を講じることはできません。最終的には検討した対策を抽出していくことになりますが、発生した事故・トラブル内容の重篤性や発生頻度により投入可能な費用は異なってきます。それらにつきましては、別の記事で優先順位の決定について解説した別の記事をご参照ください。
3.対策による防止効果を評価する
対策を検討・実施した後は対策防止効果の評価をおこないます。
完全に防止できると評価できれば問題ありませんが、不十分な場合は対策を追加する必要があります。
上記で「発生した事故・トラブル内容の重篤性や発生頻度により投入可能な費用は異なってくる」と記載しました。
完全な対策であると判断し多額の費用を投入しても、残念ながら実際に行ってみなければわからないケースも多くあります。
そもそも、事故やトラブルは、不安全行動と不安全状態が重なったときに発生します。
従って、仮に対策が不十分でリスクが残っていたとしても、重ならなければ災害は発生しません。
経営資源に乏しい中小企業では、お金をかけない”人で対応すること(管理的対策)”が取られるケースも多くありますが、”人による対策”の組み合わせでも事故やトラブルを防止することはできます。
しかしながら、対策がマンネリ化してしまうと、防止効果は半減してしまいます(=人に頼らない防止対策の信頼度が高い所以です)。
ヒトは習慣化した行動を変えたがらない傾向が強くあります。
その理由は新たな活動を展開することによる不安やエネルギーが必要になるからです。誰しも楽な法を選ぶのは当然と言えば当然です。
従って、自浄作用は期待できないため、第三者の視点を入れることでマンネリ化を打破し、対策が有効になるよう努めること、しっかりチェックしていくことが必要になります。
下記にマンネリ化を防止するための一例を記載します。
マンネリ化防止策 | 内容 |
チェック者の刷新 | これまで実施していない人がチェックします。各職場管理者の相互チェックが理想的です。 |
内容の変更 | テーマ、重点課題を設定し、ピンポイントでチェックします。 |
頻度の変更 | 通常、1回/年実施していたのであれば、チェック月間を設け、チェック頻度を増やします。 |
実施者の育成 | 研修や他社への視察を通じ、社外の風を入れるようにします。 |
【注意事項】
マンネリ化は慣れによる意識の低下と言えますので、刺激を与え続けることが有効な手段と言えます。
刺激を与えるとは、上記に記載した通り”刷新” ”変更”を行っていくことに他なりません。
しかしながら、その頻度が増えすぎると、反って”変更することの慣れ”にもなり兼ねませんので状況を見定めたうえで、刷新・変更を実施することをお薦めします。
4.従業員への意識づけを図る
どれだけ有効な事故・トラブル発生防止対策を立案しても、実行する従業員の意識が低ければ意味はありません。
例えば、機械設備で対応しても、正しく扱わなければ事故・トラブルは発生します。
無くしたとしても、ボーっとしていれば想定外のリスクが発生する可能性もでてきます。
従って、従業員の意識を高めることが何よりも重要になります。
従業員の意識は経営幹部や社長の想いで変わります。
社内での役割分担を明確にし、トップの熱意を現場に浸透させていくことが重要です。
コメント